How to explain optimization to a planner
This time I feel like writing about something that I’ve encountered in my work since I joined AIMMS over a year ago. It probably will be a shorter blog post than you’re used to, but hopefully equally inspiring.
In speaking with our business relations, I often find myself wondering how to best explain what optimization is all about. For math people, it’s easy. They will refer to a set of variables (i.e. the subjects you need to decide on) that you assign values to in such a way that the objective function (your goal) is maximized (or minimized) within the boundaries of a set of constraints (restrictions). This is formally true and it’s important to grasp the concept so you can easily go back to the basics.
But imagine you’re a demand planner – it works equally well for a supply chain planner or an operations manager – what does optimization mean to you? What does it do? How is it different? How would it make your life easier or better? The official answer would be: optimization gives you the set of theoretically best possible solutions to your planning situation. Sounds great, right? However, this typically turns into a dead-end conversation rather quickly.
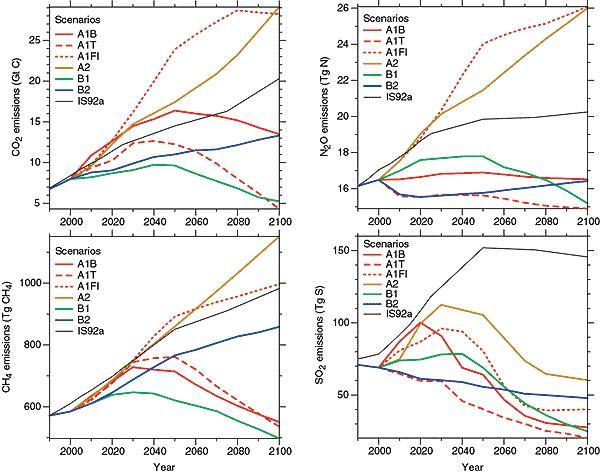
How would any system know all the complexities of my work? How does it deal with all the ‘soft’ and intangible aspects? How would I know that this ‘black box’ provides me with the right answer? And so the questions continue, resulting in a complete loss of enthusiasm or interest in any powerful technology that can help you solve complex problems.
Then, it dawned on me that a better approach was always at hand: start with the word help.
By starting with help, I mean starting with an understanding of the planner’s current way of working. Typically, he or she will create a number of scenarios in the planning process. These can be demand scenarios, but also blending scenarios, supply scenarios or production scenarios. You can easily extend that concept into other areas.
My eldest daughter, for instance, is in the process of finding a high school to enroll in for the next six years. These schools typically go through several weeks of scheduling complexity, assembling rosters that match the requirements and constraints of teachers, pupils, buildings, class composition, and all sorts of regulatory affairs.
Now back to the planner and her scenario building. Typically, a planner is happy if she has compiled one, or at most a few feasible scenarios. Recently, Oliver Wight shared with me that in the monthly process of IBP, many companies assemble one integrated scenario, and then move on to jointly address the problems and bottlenecks of that single scenario. So how can we help a demand planner, or an IBP planner, in such a situation?
How about helping her assemble 10 feasible scenarios? Wouldn’t that be a good start? And suppose these 10 scenarios can be created in a few hours instead of weeks? This is exactly what is being done right now by companies like Shell, RedeCard, Zalando, and JBS.
But the best is yet to come. These 10 scenarios are selected out of, let’s say, 10.000 scenarios that have been designed by the computer, and all of them meet the required business conditions or constraints. Selection takes place on the basis of a balanced assessment of revenue, margin, and/or utilization performance. As a planner, you then proceed by selecting your best 2, 5 or 10 scenarios – as many as you are willing to evaluate to base your next decision on.
Now if I were a planner, I would love to have a tool that would help me create this many scenarios. It would allow me to spend much more time on really understanding the impact of specific choices, the vulnerability of specific plans, and help me improve my company’s operations by making them more robust and cost effective.
Would you like to work with such a technology? Let us know in the comments.
Get a roundup of our best supply chain content every month in your inbox! Sign up for our blog digest here.