The Impact of Probabilistic Planning to Supply Chain Resilience
Understanding probabilistic or stochastic planning
Imagine you are planning an important event, but you are unsure about how many people will attend. A traditional approach might be to guess one number and prepare based on that single guess. However, if your guess is wrong, you could either have too much or too little prepared.
Now, think about planning in terms of your supply chain.
Traditional (deterministic) planning is often like that single guess – it assumes one fixed scenario for things like production volumes or inventory levels. But in the real world, many factors can change, such as demand fluctuations or supply disruptions.
Probabilistic or stochastic planning can be a more flexible and realistic approach. Instead of betting on one outcome, you consider multiple scenarios, each with its own likelihood. For example, you might want to plan for a high-demand scenario, a low-demand scenario, and a few in between, all based on the probability of each outcome occurring.
This way, you are not just preparing for one probable future but can adapt to another. Early decisions might need to be made with some certainty, but probabilistic planning also allows you to keep some decisions open and flexible until you can make a more informed decision.
Readiness to uncertainty
To understand how Chief Supply Chain Officers (CSCOs) are currently approaching supply chain design and strategy, Gartner surveyed 437 respondents from April to May 2024, which included senior managers and above from companies with annual revenues of at least $250 million across North America, Latin America, Europe, and Asia/Pacific. The data showed that risk management considerations, such as improving resilience, in addition to enhancing flexibility and agility, have displaced cost-efficiency as the top drivers of network changes (See Figure 1).
Vicky Forman from Gartner shares more insights from the survey and how CSCOs are currently approaching supply chain design and strategy.
“Supply chain leaders are moving away from an overreliance on low-cost networks and are instead focusing on diversified approaches to mitigate risks and enhance performance. While cost-efficiency is still a prominent concern, CSCOs are taking a wider view of the costs associated with the impacts from disruptions and poor levels of resiliency when making network design changes.”
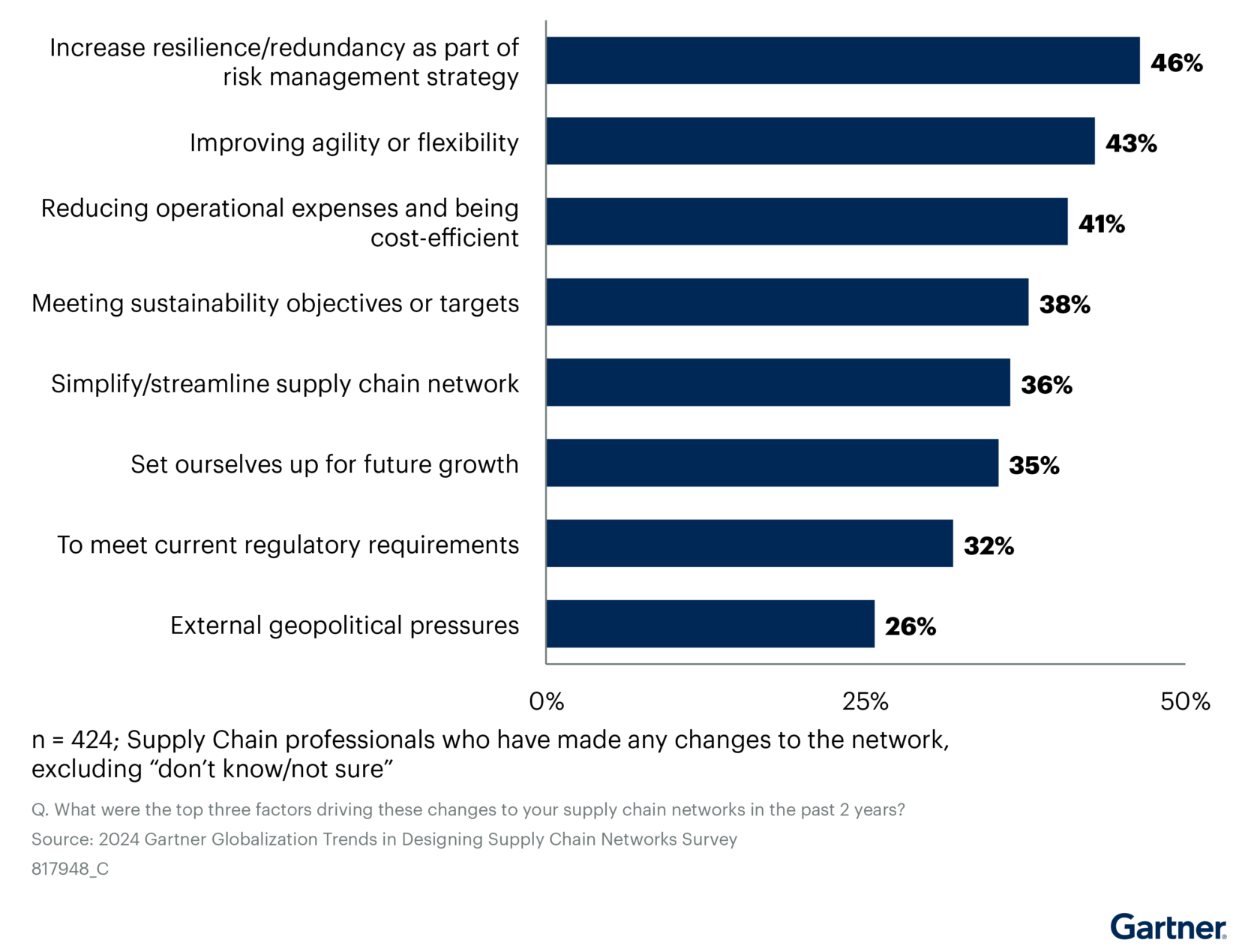
“According to the 2023 Gartner Antifragile Supply Chain Management Survey, two years from now, the number of companies changing to a planning approach within a range of probabilities will grow 23% (see Figure 2).”
“Developing this capability requires a cultural shift. Supply chain planning leaders must start to embrace uncertainty. That’s because even within a range, reality will be a point within it, and the rest of the areas of the range will be wrong.”
How do supply chain experts adapt their planning approach
Probabilistic planning in supply chains involves systematically analyzing multiple scenarios for each business objective to account for uncertainty and variability. Here is how a supply chain expert typically approaches this process:
- Define Business Objectives: The first step is to clearly define the key business objectives that need to be met. These could include objectives like minimizing costs, maximizing service levels, optimizing inventory, or ensuring timely deliveries.
- Identify Key Uncertainties: The expert identifies the key uncertainties that could have a significant impact on these objectives. These uncertainties might include factors like demand fluctuations, supply delays, transportation disruptions, or market price volatility.
- Develop Scenarios: Based on the identified uncertainties, the expert develops a range of scenarios. For example, they might create scenarios for high, medium, and low demand, or for varying levels of supply chain disruptions. Each scenario represents a separate set of conditions that could impact the supply chain.
- Assign Probabilities: Each scenario is assigned a probability based on historical data, market trends, and expert judgment. These probabilities reflect the likelihood of each scenario occurring.
- Model the Scenarios: The expert uses mathematical models to evaluate the impact of each scenario on the business objectives. The modeling approach can have a significant impact on the solution, so it is important that the selected model is appropriate for the business question.
- Analyze Trade-offs: The expert then analyzes the trade-offs between different scenarios. For example, they might assess the trade-off between holding higher inventory levels to mitigate the risk of stockouts versus the increased carrying costs associated with that strategy. The goal is to understand how different decisions are made across a range of scenarios.
- Create a Stochastic Plan: Based on the analysis, the expert develops a stochastic plan that balances the objectives across all scenarios. This plan includes flexible strategies that can adapt as actual conditions unfold, such as contingency plans, dynamic inventory policies, and responsive supply chain tactics.
- Determine the Value of the Stochastic Planning Approach: A stochastic plan may often seem more expensive than a deterministic plan. This is because the solution found through a stochastic approach is usually robust to all sorts of perturbations among uncertain parameters, e.g., the solution should be feasible for a high-demand and low-demand scenario, whereas a deterministic solution is only optimized for one scenario. To determine this solution’s value, experts evaluate the cost of these perturbations on the deterministic solution that was calculated based on the expected value of the uncertain parameters.
- Continuous Monitoring and Adjustment: Probabilistic planning is not a one-time activity. The expert continuously monitors actual performance and compares it to the scenarios. As new data becomes available or as the environment changes, they update the probabilities and adjust the plan accordingly. This dynamic approach ensures that the supply chain remains resilient and responsive to changing conditions.
- Decision-Making Support: Finally, the expert uses the insights gained from the stochastic analysis to support decision-making. They provide recommendations to leadership on which strategies to pursue, based on the likelihood of different scenarios and the associated risks and benefits (value of the stochastic planning approach).
Let’s see how this looks in practice. SAP has joined forces with the Technical University of Munich to investigate what a more resilient supply chain plan means for our customers and how such a solution could look like in the future.
What are SAP gains after implementing this model?
- Profit implications of decisions including the risk of profit below a certain level (in EUR, US$, etc.).
- Resilient decisions, i.e. being able to adapt to different futures by jointly considering multiple future scenarios (incl. probabilities).
- Ranges for future decisions (as a spread around a single-value base plan) to prepare for potential adjustments early on.
- Possibility to influence future product decisions for SAP IBP (depending on customer feedback on the results of the project).
Ready to find out how to optimize your supply chain for resilience? Talk to our experts today!