How Costly are Supply Chain Disruptions and How to Mitigate Them?
Supply chain disruptions are broadly defined as a business’s inability to receive, produce, ship, and sell products. The two fundamental issues identified are disruptions in manufacturing production and rising transportation costs.
Disruptions caused $1.6 trillion in missed revenue
Accenture conducted a study to understand how businesses handle disruption in engineering, supply, production, and operations. They surveyed over 1,200 senior executives from 11 industries to assess their investment and maturity in these areas. The study found that disruptions caused companies to miss 7.4% – 11.0% revenue growth opportunities. Industrial equipment manufacturing was the industry that was impacted the most.
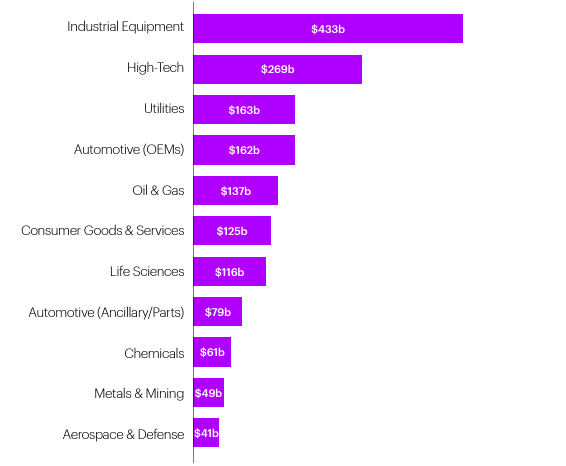
Lost revenue significantly impacts a company, creating a domino effect of challenges. It immediately hinders growth and investment opportunities, casting a shadow on future ambitions. For employees, this translates into resource constraints, potential job insecurity, and halted personal growth, leading to a decline in morale. This situation paints a grim picture of unfulfilled potential and strained professional and personal lives, underscoring the profound importance of financial stability for a company’s health and its people’s well-being.
On the other hand, companies with higher resiliency maturity were more successful, capturing 3.6% more revenue than those in the bottom quarter. These resilient companies also enjoyed a 1.2 percentage point higher EBIT margin compared to less resilient ones.
The ability to measure impact is proportional to supply chain resilience
Resilient companies are alerted to disruptions faster, meaning they also understand, react to, and recover from disruptions earlier.
Accenture’s report mentioned above reveals that the average time from being alerted to a disruption to recover completely takes three months, and it can even reach five months. For 57% of companies, it takes more than a week to be alerted to production or supply network disruptions. Even then, almost 80% of executives say it takes an additional week or more to assess the disruption’s impact.
For many supply chain decision-makers, managing disruption is becoming a day-to-day issue. According to the Deloitte Global Survey of over 1,000 supply chain executives, nearly 80% have faced adverse supply chain events in the past year, with causes ranging from geopolitical tensions to climate events.
However, only about 22% strongly believe their supply chains have been resilient against these disruptions.
The key differentiator for resilience appears to be the use of metrics to measure effectiveness in responding to supply chain disruptions.
Those employing clear response metrics are 3.4 times more likely to report successful management of external shocks compared to those without such metrics. This pattern holds true globally, suggesting that clear metrics enable leaders to understand better and respond to disruptions.
What could you do as a supply chain leader?
Investing in the right mix of resiliency capabilities leads to minimizing the cost of disruptions. You can:
- Improve your maturity and resiliency in key capabilities, enhancing your ability to use disruption to your advantage.
- Invest in visibility, predictability, and continuity-focused technology.
The Accenture study measured maturity across 30+ capabilities that enable resiliency in engineering, supply, production, and operations. After carefully looking at all, these are the capabilities that point to the most critical areas where companies should prioritize investment:
- A collaborative approach to digital twin platforms.
- Eco-design approach to embedding sustainability by design (e.g., carbon footprint, circularity).
- Continuous upgrade of offerings to adapt to customer needs (e.g., product services upgrades, product features upgrades based on over-the-air).
- Dynamic and data-driven planning with “what-if” scenario modeling capabilities.
- Predictive early detection of operations issues (poor quality, breakdowns, maintenance needs, non-conformity).
- Multi-tier supplier network, with physically closer partners and contingency plans.
- Use location risk analysis to automate ‘what-if’ scenarios using data on climate, conflict, and geopolitics to foresee and mitigate impacts on your profitability and operations. A company nowadays must stay ahead of disruptions and safeguard its business’s future.
- Structured analytics to predict surge or decline in demand (in addition to customer historical forecasts).
- Proactive customer segmentation to arbitrate demand in case of shortage.
At AIMMS, we share the following framework to guide our customers on how to deal with disruptions, which is very much in line with the findings discussed above.
We recognize the challenges associated with allocating time and dedication to change processes, particularly as organizations grapple with the repercussions of recent disruptions.
AIMMS and our extensive global partner network possess specialized expertise in aiding companies as they navigate and evolve within this sector. Our role extends beyond enabling supply chain teams to develop internal competencies; we also offer help identifying the most suitable partners for outsourcing needs.
Recap (TLDR)
To wrap up, supply chain leaders need to understand,
- The importance of being proactive and anticipating events
- How to respond best to minimize cost and disruptions impact
- Specialized vendors like AIMMS work with an ecosystem of partners to support implementation teams and get all the weight off their shoulders.
Discover firsthand how AIMMS can assist you in addressing disruptions and reducing costs within your supply chain.