Tata Steel Drives Supply Chain Transformation with Optimization Technology
Tata Steel is one of the world’s largest steel producers. In fact, it’s very likely that Tata Steel plays a role in your life today, by providing raw material for the car you drive, the house you live in, and the roads you drive through. The company was established in India as Asia’s first integrated private steel company in 1907. Today, the steel manufacturing leader has an ambitious digital transformation agenda and is leveraging AIMMS technology to optimize operations in its home country.
We spoke with Deblin Chakraborty, Senior Manager at Tata Steel’s Analytics & Insight team, to hear more about this initiative.
1. Deblin, could you tell us more about yourself and the division you work for within Tata Steel?
I work for the analytics department within Tata Steel. Our analytics department is comprised of data scientists who work on developing AI models, as well as OR specialists who focus on supply chain optimization, simulation, and mathematical programming. I belong to this second division and work mostly on mathematical modeling, simulation, and supply chain analytics.
2. When did you join Tata Steel?
I have been with Tata Steel since the beginning of 2018. Before joining Tata, I worked with other steel manufacturing companies, like Jindal Steel. I have about eight years of experience in the industry, in both operations and analytics roles.
3. Your team is currently using AIMMS for a supply chain optimization project. Can you tell us about your goals?
We are using several AIMMS-based models to improve our operational efficiency, with a focus on India. Tata Steel uses a lot of advanced software to tackle business requirements, but spreadsheets are still the preferred choice in most cases. Before we introduced AIMMS, we had a more conventional way of doing things, using spreadsheets. However, the supply chain problems we face in the steel industry involve a lot of different variables and are often difficult for the human mind to fathom. We needed to challenge the traditional way of doing things and push ourselves beyond the use of spreadsheets. We were able to do that by using AIMMS. With the output from AIMMS models, we can improve our decision-making process. For instance, we use AIMMS to optimize production capacity, understand which raw material should go to which manufacturing facility, maximize yields in different plants, and streamline our logistics.
4. Were you using other tools aside from spreadsheets, before using AIMMS?
We were using point solutions in some units to carry out optimization, but not in all. We were mostly using Excel to do manual calculations.
5. Why did you choose AIMMS specifically?
BCG (an AIMMS partner) played a big part in introducing AIMMS to TSL. We also did an extensive comparative study of various optimization software vendors but eventually decided on AIMMS, as it matched our requirements. The plethora of functionality and solver options available in the AIMMS Platform address the requirements of our steel manufacturing plant. The software supports scalability. Additionally, problem handling using solvers is very much advanced in AIMMS.
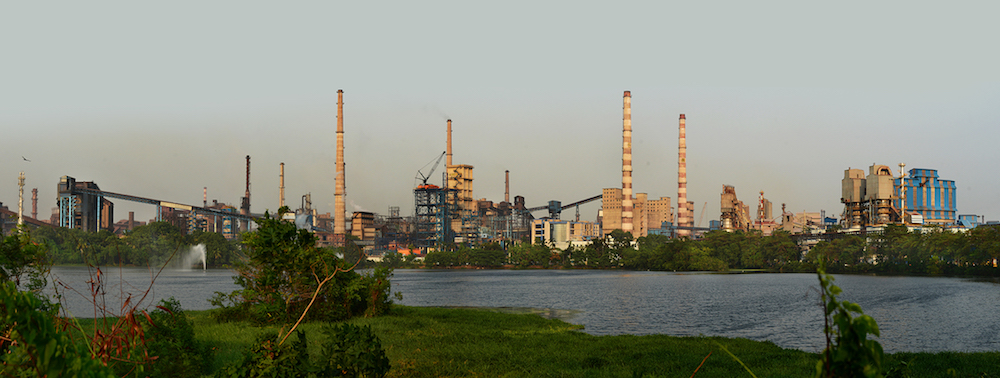
6. What made it the right time to change?
Our management team has a very clear digitalization agenda and is investing heavily in AI and the future way of working. It was very clear that we needed to move away from spreadsheets. In fact, we’re building towards a situation where data will be automatically fetched in the background from our ERP and loaded into the optimization models. All our operations will be automated and optimized, with as little human interference as possible. AIMMS is playing a big part in this digital revolution within our company.
At first, we were interested in using AIMMS mainly as an optimization solution, but we realized we could do more to harness its full potential. That’s why we’re building up our AIMMS capabilities internally.
7. How many people use AIMMS within Tata Steel at the moment?
Multiple departments are using AIMMS-based models for optimization now, including our planning and scheduling team, marketing, and inbound and outbound logistics. We have approximately eight to nine AIMMS models in use, and five people developing in AIMMS. We want to increase that to 20 people. Your support team has been very helpful to get the training we need to make this happen.
8. Aside from facilitating access to training, how are you handling change management internally?
Changing people’s mindset is always the most challenging part and it’s a tough job to do. But it’s helped that our management team is invested in a digital transformation agenda. Our team is, for the most part, open to trying new approaches and technologies too. For instance, I often get requests from people who would like to start using AIMMS to optimize a part of the business. I would like to thank our management for this. They are very supportive when it comes to accepting newer technologies and solutions. Since change management needs to be supported from top down, it would not have been possible without their encouragement.
So, I would say that we’re still in the change management process and haven’t fully reached our goal, but the direction set by our management team is clear and our team has the support it needs to embrace transformation.
9. You mentioned that you’re moving to a more automated way of doing things and that AIMMS is playing a big role in this process. Can you tell me how you see the use of AIMMS evolving?
Currently, there is an interface for end users which is used to solve optimization problems using input data. There is still a lot of human intervention involved in this process. What we’re doing now is developing an API for AIMMS, where an automated program will call the API and ask AIMMS to do all this stuff by itself.
The bottom line is maximizing value for our organization, and AIMMS is playing a big role in helping us streamline a lot of our processes. For example, we can now ask people to focus on other things instead of doing repetitive jobs in Excel.
10. What are you most proud of about your AIMMS project?
We are proud to see that AIMMS is delivering results that directly resonate with our objectives, like bringing down our cost of production. But I am also proud of the fact that this project has the potential to transform our way of working at Tata Steel.
Ready to optimize your supply chain like Tata Steel? Explore the potential of AIMMS and take your operations to new heights.